On April 1, 2017 Oakwood’s S.T.E.A.M. program demonstrated its prowess when it walked away from the Hydrogen Horizon Automotive Challenge with not only a first place for best design, but also a first place in the race itself with an incredible 254-lap lead on the second place team. This event, the culmination of an 8-month program sponsored by Toyota to promote awareness of renewable energy and the benefits of using hydrogen in an automotive setting, was held during the National Science Teachers Association Convention. To read about the science behind Oakwood’s impressive wins, continue below for the full story and images and video from the event.
Collaboration & Innovation Fuel Oakwood Victory
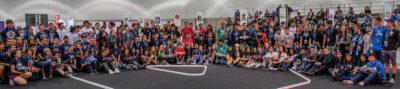
When Horizon decided to get into the Hydrogen energy business in 2003, cars powered by hydrogen fuel cells were still in the future. Rather than join the race to make a battery and H cell that could power a full-sized vehicle, which didn’t come to market until 2015, the company decided to invent a much smaller unit—0.07 volts. This technology got picked up by the education market and, as a result, Horizon has provided fuel cells to more hydrogen-powered cars than any other maker on the market. They just happen to be of the RC variety.
One of the main drivers behind this success in the world of diminutive hybrid race cars is the Hydrogen Horizon Automotive Challenge (H2AC), a STEM competition for high school students to design, build, and race their own hybrid hydrogen- and battery-powered 1/10th scale RC cars powered by the company’s fuel sticks. The four-hour endurance race has taken place across Europe and in Florida for the past three years, and opened a separate competition in Southern California in 2017. Oakwood was excited to participate, along with nineteen other schools.
Horizon provided each school with a starter kit including A 30W fuel cell and control board, seventeen hydride Hydrostiks, high-end chassis kit, motor and pinion gear, rechargeable battery and charging station, and a standard wheels/tire set. While the only thing the schools were required to design and build was the car body, they were given the opportunity to adjust or replace any of the other car components, with the exception of the “brain,” the control board that runs the feedback between the hydrogen sticks and battery, and the fuel sticks themselves.
The goals of the competition were tied to these car components in more ways than speed. There were six separate competitions for the students:
- Endurance
- Fuel efficiency
- Car body design
- Pit design
- Innovation
- Video on eco living
By adjusting or replacing certain components, and then putting the final product through rigorous testing and data gathering, the teams could optimize their performance at the final race, which would take place April 1st at the Los Angeles Convention Center. The Oakwood team planned to focus on the first five categories, deciding that they would let the video component go in favor of spending more time perfecting their car and race-strategy.
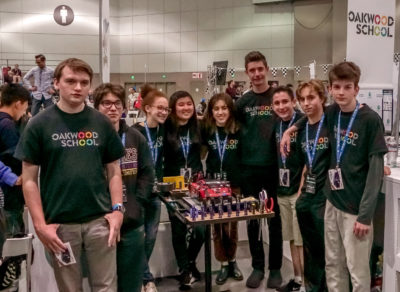
The nine students on the H2AC Oakwood team, all hand-picked for the project by STEAM department chair Marcos Arias, were excited to get started on the car design, but first they needed to learn more about the science that would be fueling the engine, and the broader global impact of renewable energy. Sarah Wardlaw, one of Oakwood’s middle and high school science teachers, gathered the students after school one or two days a week for several weeks. The team had a range of ages, so Sarah empowered the older students to mentor the younger ones and help explain the concepts and work through the experiments. They discussed global warming and how to capture and store energy, including a demonstration of hydrolysis, which is the basic principle behind charging the hydro sticks. Oxygen is liberated from the water molecule and released into the environment, while the hydrogen goes into the sticks, creating a range-extender for the battery. The stick is then plugged into the fuel cell, where the electrons on the hydrogen molecules are stripped away to generate an electrical current. The hydrogen then recombines with the electrons and an oxygen molecule to become waste water. The electrical current that is fed into the RC-car battery from this process can extend its life by over half an hour. Figuring out how to maximize that battery extension, through adjustments in speed, efficiency, weight, and car design, was the primary goal of the competition.
Once they had the science under their belt, the students had three months to design, build, test, and rebuild their car, as well as the pit they would use in the final race. Marcos divided the students into teams so that they would be able to go deep into their specializations, rather than everyone having a general knowledge of the full process. Hannah was the project manager, in charge of data collection and analysis. Seth and Alea researched what battery option would work best, and came up with the pit design and tool organization. Sophie and Luke designed and painted the car body as well as a new Hydrostik mount. Harrison and Hank oversaw the car itself, adjusting the parts and design and making sure everything was maintained in working order. And Eric was the main driver, along with Luke and Harry. Marcos knew that come race day, these teams would need to act autonomously. He wasn’t just helping them make the best car and gain an understanding of the underlying technology, he was enabling them to run the race without him, managing everything from battery and fuel stick changes, to problem solving potential errors and crashes, and adjusting their race-strategy on the ground in response to real-time data.
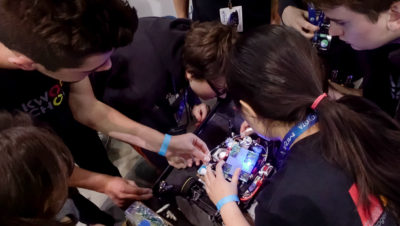
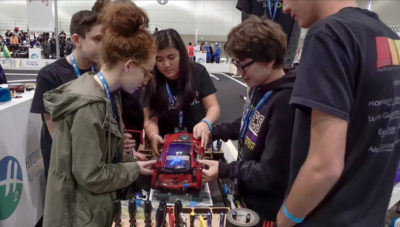
The Car & Pit
The team designed several iterations of the car and its components before they landed on the final design.
The hydrogen fuels stick mount that came with the H2AC kit was problematic from the beginning. “The fuel stick mount was originally located on either side of the fuel cell and took four screws to remove,” Sophie explains. “We changed it to a single mount on the side of the car. And we changed the x-tube connector to a single connection point so it can be removed as a single pack.” Sophie and Luke completely reimagined the mount and designed a Velcro attachment mechanism. Though the redesign took the better part of two months to perfect, in the end it shaved the Hydrostik change-out time to just a few seconds.
The batteries were another part that required replacement. The type sent in the kit was heavy, and weight was one of the main factors that would affect the car’s efficiency and speed. Seth and Alea knew they could find a better solution. After testing several batteries for power, weight, and lifespan, they chose a set of “shorty” Lipo batteries, which provided the most power while keeping the weight at a manageable level. They also tested a couple of different battery mounts to find the most efficient and compact option.
For the car itself, the team tried to use the chassis provided in the kit, but it was clunky and inefficient. “First we tried to modify the car that the H2AC folks sent to fit our battery and fuel stick mount,” Seth explains, “But we decided that it was undriveable. We had to stack the components in such a way that it had a really high center of gravity.” Hank, who had experience with the engines and builds of real cars, applied that knowledge to redesigning the chassis of the RC car, perfecting the suspension and weight distribution, and making improvements to the motor, steering, and gear rotation.
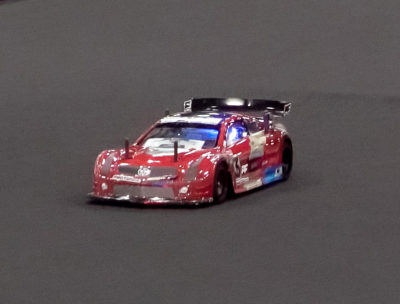
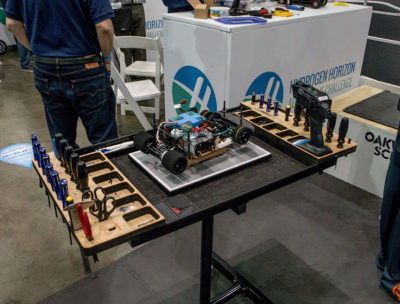
Harry and Harrison formatted the base board that would hold the components. For the board, he needed a material that would be flexible and light, but strong enough to withstand the stress and potential crashes of a four-hour race. After testing a few materials, including the original board included in the kit and a custom design made from delrin, he ended up laser-cutting the final version from Masonite, a wood composite. “We made a template,” Harry explains, “And then slowly cut it down to lose as much weight as possible so that the car would handle more easily.” Once all the components were ready, Hank, Harry, and Harrison arranged them on the board and soldered them in place, along with a car kit for the frame and wheels.
Meanwhile, Sophie was hard at work designing the shell for the car. The team ended up going for a classic race-car look in bright red, with an eight-layer paint job. The bumper for the car, which would sustain the most impacts during the race, was fit with a foam core molded to its exact dimensions to prevent cracks.
In the end, the team had a car that was engineered and tuned to the point where it didn’t consume a lot of energy. It was one pound lighter than any of the other cars at the same scale in the race—2,600 grams vs 1,900 grams. That difference in weight would end up making a huge impact on the team’s performance on race day.
Beyond the car itself, the design of the racing pit would determine how efficiently the team could fix and maintain the car during the race. Alea and Seth came up with a custom pit design akin to an operating table, with designated slots for each of the tools. There would be no scrambling to find the right pliers or screwdriver during a critical moment. The pit was so organized that the car mechanics would practically be able to work blindfolded.
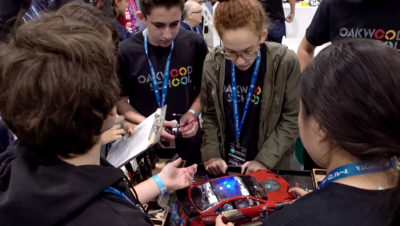
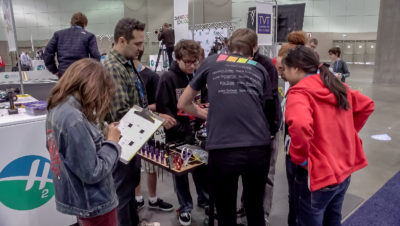
Trouble Shooting
Once the students were pleased with the car’s design, they needed to continue to test it, to work out as many kinks as possible before race day. Marcos underlined for them that “a thousand little things add up to success.” It’s not just about making the fastest car. All of the components need to work together to make it the best.
This became apparent as they put the car through its paces. Several problems came up that would cause lengthy pit times during the race. The first was a pin-sized leak in the air line. It was apparent that something was wrong when the fuel cell suddenly stopped charging the battery for more than five to ten minutes. Once the students discovered the leak, located in the exhaust line, they fixed it. In the process, they were surprised to discover that they were working with a closed system. Even though the leak was not in the input line, it still caused the system to malfunction.
Another glitch occurred when the pressure regulator wires bent and disconnected inside of their wire coating, causing the fuel cell to shut off due to a low pressure reading, even though the sticks were full. The problem was hard to spot, but once the team stripped the wires the solution was evident. They needed to build a more durable design for the wires, which had disconnected due to repeated use.
The final component that the team tweaked was the order in which they used the fuel sticks. It turned out that the seventeen sticks that H2AC sent with the car kit were not created equally. Each stick should have contained a full gram of hydrogen when fully charged, but when the students weighed the sticks, they found slight variation in the volume. So they organized the sticks by weight, with the fullest at the front of the line. By using the best sticks first, the team optimized their pit times in the race.
Data Analysis
Driving during a four-hour endurance race is quite different than during a typical RC race, which lasts only five minutes. The drivers, Eric, Luke, and Harry, needed to adjust their racing style for this long-haul race in which success would be determined by a host of factors, not just speed. Their practice runs also provided the data needed to fine tune both the car design and their performance. Hannah, the pit manager, tracked the data collected from the practice runs. “We collected data over the course of the practice runs,” she explains, “including tracking the fastest laps and comparing that information to modifications on the car. We looked at how the weight of the Hydrostik fuel system impacts how the car runs. We also wanted to explore how different drivers can affect lap times, and how fast the car runs out of energy or hydrogen.” All of these bits of information helped Hannah determine how to optimize the car’s performance over the four-hour race. Based on the results she plotted out a chart based on fifteen minute intervals, with optimal pit times. They found that with the right combination of Hydrostik, driving style, and car design, they could extend the battery life to an hour and forty-five minutes, a huge improvement over their initial tests, when the battery lasted only 35 minutes on average.
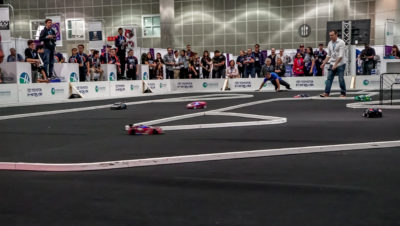
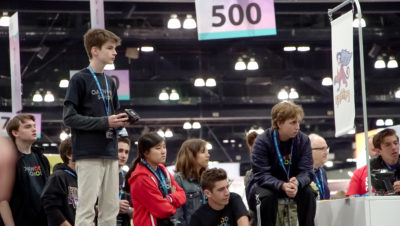
Race Day
Race day arrived and the students were excited to get started. As the other nineteen teams joined them at the Los Angeles Convention Center, they sized up the competition. The cars were all unique—it was clear that the teams had put a good amount of effort and imagination into the body design—but it was impossible to tell what modifications they had made under the hood. They would have to wait for the race to start to find out!
Eric, the lead driver, had perfected his racing style. Though he had a lot of previous experience in racing RC cars, this was a different beast. The races he was used to consisted of short bursts of speed on a clay track where you battled with the other drivers towards the finish line with little regard for the car’s battery. This was a flat, rubberized track, and he had found that going as fast as possible had consequences over the long haul. The battery drained faster and you were more likely to crash, either with another car or along the track wall, which might result in a longer pit time to fix any damage to the car. Driving at a fast but steady pace was the best approach.
Marcos didn’t know what to expect from the other teams in the competition, but he was confident that his team was ready for any challenges they might encounter. They had tested, redesigned, and refined their car and race-day process to the point where he knew they didn’t need his assistance. He was only allowed to check in every hour during the race, so any problems that came up were in their hands.
In the end, the team and car lived up to every expectation. There were no major malfunctions and the team dealt with the few problems that came up efficiently, getting back on the track in under a few minutes each time. For example, when the custom bumper developed a crack, the spoiler along the edge came out of alignment, affecting the aerodynamics. Rather than try to patch it up, the team opted for a much simpler solution—they quickly trimmed it off and rejoined the race.
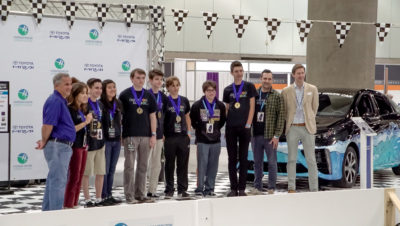
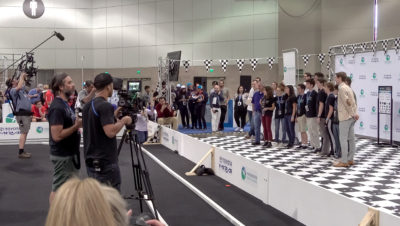
With the testing and preparation, it was no surprise that Oakwood ended up taking home the prize for fastest race. But how much they won by was staggering. The next best team was a whopping 254 laps behind Oakwood! What does a team do when they are up by an insurmountable margin? They stop trying to win—that’s already been accomplished—and focus on other factors. For Oakwood, that meant bringing their efficiency, rather than speed, to the forefront. They slowed down during the last hour of the race, causing their voltage consumption to go down by half. In the end, the team only used eight of the seventeen Hydrostiks, a significant accomplishment.
The Oakwood team also won the prize for car design, a tribute to their innovative, aerodynamic, and appealing approach to the car body.
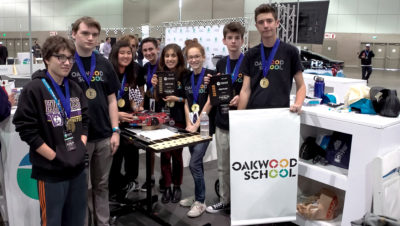
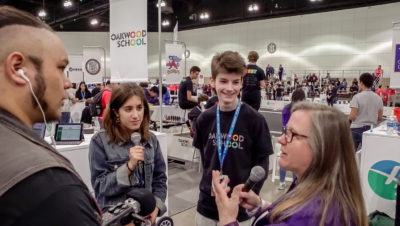
What’s Next
This is just the beginning for H2AC and Oakwood. The race is expanding to five states next year, opening the possibility for a national competition. Marcos and Sarah will be working with H2AC to take a closer look at the rules and award categories to make sure the efforts and results of the teams are measured correctly. The next Oakwood team will be able to tackle some of the innovations and goals that they had to put on the shelf for this year’s competition, including using telemetry to increase the live feed of data from the car, and a new design for the battery. The bar has been set high, but Oakwood’s students are prepared to meet the challenge again!